General information about Siemens SGT-100 turbine
The SGT-100 is a Siemens industrial gas turbine with a capacity of 5.05 to 5.7 MW. Another name for this turbine, used earlier, is Typhoon. SGT-100 has a simple, reliable and compact design. It is available in single-shaft and twin-shaft versions.
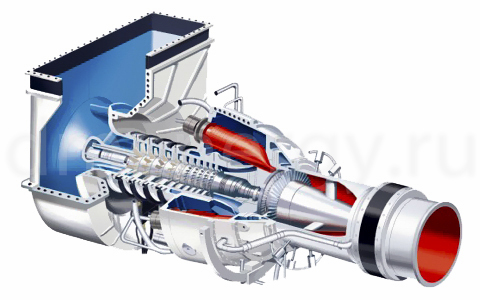
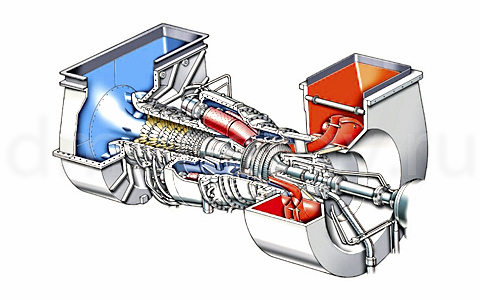
Advantages
- High operating stability
- Favorable price-power ratio
- Excellent load intake and load shedding performance
- Excellent load intake and load shedding performance
Convenient and easy maintenance (quick replacement of the gas generator; multiple boroscopic openings; air intake hood with both vertical and horizontal connector; easy access to к combustion chamber, igniters and flame tubes) - Quick shutdown of the unit
Areas of application
- Simple cycle
- Combined cycle
- Combined heat and power generation
- Power generation in the oil and gas industry on offshore platforms and floating oil production systems
- Mechanical drive of pumps, compressors (twin-shaft version)
SGT-100 turbine is equipped with a combustion system capable of burning various types of fuel – from artificial gas, close to natural gas in its characteristics, to exhaust gases (including garbage, boiler and sewage gases). The electrical energy generated is utilized by the customer or exported to the local utility grid. The waste heat from the exhaust gases can be recovered and applied to other processes to maximize overall thermal efficiency.
Design and specifications
The SGT-100 single shaft turbine has a very simple design – it consists of a double bearing rotor in a high strength casing.
The twin shaft version of the turbine includes a gas generator and a cantilever turbine.
The figure below shows a cross-section of the internal circuit of the SGT-100-1S turbine engine.
- – 10-stage axial compressor
- – 4 adjustable guide apparatuses
- – DLE-type tubular-ring combustion chamber
- – 2-stage compressor turbine
- – V-shaped teeth
- – spacer bolt
The SGT-100-1S turbine engine internal circuit, shown in the figure above, includes a near-sonic 10-stage compressor.
The compressor’s two-stage turbine drives the compressor with excess torque drawn from the generator via the input shaft.
The turbine is configured with either a conventional combustion system (diffusion flame) or a DLE system. The former provides for a variety of different fuels, while the latter reduces the exhaust gases emitted into the atmosphere.
The guide apparatus and blades are internally cooled and made of very robust material, which allows the turbine to operate in the harshest conditions.
Adjustable guide apparatuses in the compressor section are used to optimize the start-up and normal operation of the compressor. This feature has the added benefit of reducing air flow and element loading, as well as keeping carbon monoxide, CO, levels low.
Dual ignition and cross ignition of the remaining combustion chambers is a feature common to conventional combustion, while the DLE system requires an ignition source in each of the combustion chambers.
The turbine is monitored via a control system based on a programmable logic controller. The system provides control at all stages of operation, from start-up to interventions during scheduled shutdown. The design of the turbine control module allows it to be integrated into the overall plant control system.
Intensive technical progress accelerates the obsolescence of gas turbine equipment. And despite the excellent technical performance of the turbine at the time of its release, as the years pass, the plant may need to be modernized. DMEnergy provides modernization, maintenance, repair services, and a wide range of spare parts for Siemens SGT-100 gas turbines. Our high quality service will help to significantly improve the efficiency and performance of your turbine.