- Basic information about Siemens SGT-200 turbine
- Design and technical characteristics
- Operating principle
- Equipment and application areas
Basic information about Siemens SGT-200 turbine
SGT-200 (old name Tornado) is a Siemens industrial gas turbine with a capacity of 6.8/7.7 MW, using various fuels. The turbine is characterized by excellent reliability and excellent weight-to-power ratio.
The SGT-200 turbine is a unique combination of proven reliability and new technologies. In December 1983, Ruston (now part of Siemens) was awarded the prestigious British MacRobert Prize for the Tornado turbine, which is given to the most promising innovations.
The SGT-200 has fully justified the high trust placed in it with millions of hours of efficient operation. To date, more than 430 SGT-200 turbines have been sold. The total operating time of the turbines delivered is approximately 30 million equivalent hours.
Advantages
- High operational stability
- Economic efficiency
- Low emission combustion chamber for gas with Dry Low Emissions (DLE) system
- Single lubrication system
- Easy transportation and maintenance
Design and technical characteristics
Siemens SGT-200 gas turbine is available in single-shaft (6.8 MW) and twin-shaft (7.7 MW) versions.
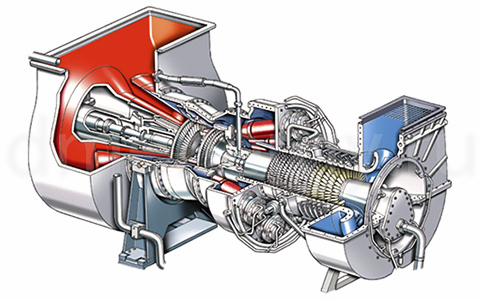
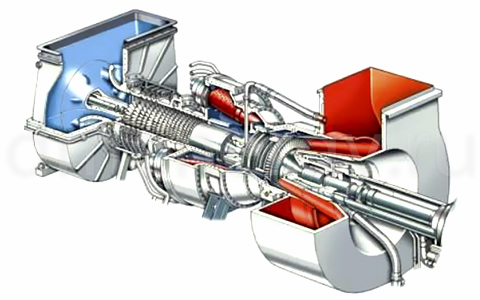
The single-shaft version consists of compressor, combustion chamber and turbine, as well as high-strength casings. This simple design allows full turbine maintenance on site. Excellent load response ensures stability in all applications.
The twin-shaft version has both a high-pressure turbine (HPT) and a free turbine. The twin-shaft version is characterized by flexibility in controlling the main operating parameters of the turbine.
Siemens SGT-200 turbine can operate on both liquid and gaseous (including hydrogen) fuels, dual-fuel combustion chamber operation mode is also available.
Compressor
15-stage near-sonic axial compressor. The stator and rotor blades are made of 17-PH steel. The compressor is equipped with a rotating diffuser. The compressor housings are separated both vertically and horizontally.
Combustion chamber
The combustion chamber consists of 8 cross-ignition counterflow tubular chambers. The chambers are accessed by separating the housing. The chamber can be removed by removing the burner. Thus, disassembly is carried out without disturbing any pipe connections.
Turbine
The first stage nozzle and impeller blades are air-cooled to ensure the required 40000 hours of operation.
Power turbine
The design of the power turbine is similar to that of the TVD and consists of two stages of nozzle and working blades.
Principle of operation
Air enters the filter and passes through the volute.
Through the guide apparatus , the air stream enters a 15-stage axial compressor where the air is compressed with a ratio of 12.3:1.
The fuel-air mixture formed by mixing with the fuel is continuously combusted, driving a turbine.
The hot gases are discharged through the exhaust system and can be used in the HRSG.
Equipment and applications
Single-shaft version of the turbine is used for power generation and cogeneration in simple and combined cycle plants; offshore and onshore facilities of oil and gas industry.
The twin-shaft version of the SGT-200 turbine is designed to drive pumps and compressors, i.e. to operate as a mechanical drive.
The turbine, auxiliary gearbox, control system and lubricating oil tank are housed on a steel turbine frame. The driven units, including the gearbox, are mounted on a separate frame, which is connected to the main frame.
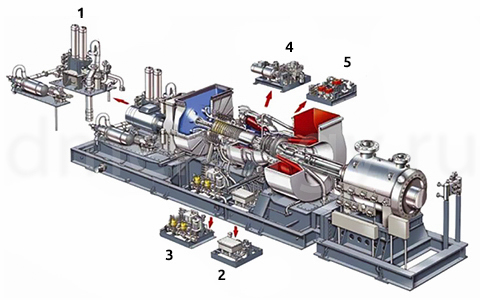
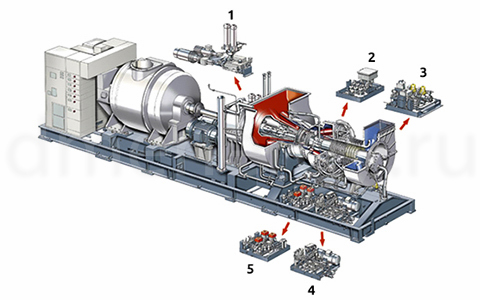
- Lubrication module
- Automatic drain module with electronic control unit
- DLE gaseous fuel module
- Liquid fuel supply module
- Liquid fuel purification module